Colchester Mascot 1600 Lathe - Page 1 email: Colchester Mascot 1600 Lathe page 1 Clausing 17' Models 8050, 8051, 8052, 8053, 8054, 8055 A Handbook & Parts Manual is available for the, the later and the As the first production Mascot 1600 left the Colchester Lathe Company's Essex works on November 20th, 1965, it marked the beginning of a six-year period that would see a almost complete overhaul of the Firm's products. The heavy 8.5-inch (215 mm) centre height (17-inch/433 mm swing) Mascot was unlike any machine the firm had produced before and marked a revolution in styling and specification; though it may have lacked mechanical novelty the lathe was reminder that even machine tools are subject to the vagaries and whims of fashion for, with its distinctive, angular appearance, ergonomically-designed controls and bright finish, it immediately made its competitors look distinctly dowdy and old-fashioned.
It would be unfair, however, to dismiss the Mascot 1600 as a mere styling exercise for this lathe was sold in an important and profitable (though demanding) section of the market - and to succeed it needed to be tough, well-made, reliable and with a combination of capacity, speed and ease of use that backed up its contemporary appearance. Induction hardened and ground-finished as standard, the bed was 13.5 inches (343 mm) wide and of the usual Colchester V-and-flat type, with separate pairs of ways for the carriage and tailstock. It was available in four lengths that gave 40, 60, 80 and 1000 inches (1000 mm, 1500 mm, 2000 mm and 2500 mm) between centres.
All the beds could be had either with or without a detachable gap piece that, if fitted, allowed material up to 28-inches (711 mm) in diameter and 8.5 inches (216 mm) thick to be swung on the (optional-extra) 17-inch and 27-inch (433 mm or 685 mm) diameter faceplates. Because it sat on a flat section of the bed instead of a continuation of the V ways, the headstock was provided with a mechanism that allowed it to be adjusted laterally - though before altering the factory setting the owner was strongly cautioned to consult the (very comprehensive) owner's manual. Designed in conjunction with the British Machine Tool Industry Research Association the headstock spindle could pass a 3-inch diameter bar and had a hardened 8-in D1 Camlock nose; all the gears in the headstock (and not just those responsible for the main drive as on less heavily stressed Colchester models) were hardened and ground finished on Reishauer machines.
Colchester Mascot 1600 Manual Woodworkers Supply
16 speeds were available, from 20 to 1600 rpm and, because of the high top speed and the capacity of the lathe, the makers warned against other than the use of the dynamically balanced, ductile-iron chucks with hardened scrolls that had been specially commissioned from Burnerd; if you want to mount a new chuck on your Mascot 1600 it would be unwise to fit anything other than one recommended by a reputable Western manufacturer. You are welcome to for advice as to what might be suitable, Concentrically mounted paddle levers on the front face of the headstock selected the spindle speeds and worked through an ingenious and compact mechanism, with (for a machine tool) an almost foolproof system of colour coding to indicate the settings. The very first lathes were listed as being powered by a 7.5 hp (5.6 kW) motor but this proved to be inadequate and much a more powerful 12.5 hp (9.3 kW) unit was soon made standard The motor was mounted inside the headstock-end plinth on an adjustable plate and drove up to the headstock through 4 V belts into a shaft on which were mounted two easily-adjusted, oil-immersed, forward and reversing clutches. On the same shaft, at the opposite end to the input pulley, was a Matrix multi-disc brake; it could be adjusted so that, in production work, the spindle could be brought to a very rapid stop or, for ordinary use, set so that the braking effect was less pronounced and the workpiece was able to be 'inched' round by gentle use of the control levers. Once the spindle speeds had been selected and the motor switched on by the headstock-mounted push-button starter the spindle control was by two levers: one pivoted from the right-hand apron wall and the other up against the inner face of the headstock; both worked through a 'third shaft' (parallel and below the feed shaft and leadscrew) that was connected by links to a cross shaft that passed through the bed just in front of the headstock. The apron lever gave a stop, forward and reverse action the other just a reverse and stop; in conjunction with the headstock-mounted clutches, the brake and electrical switches this easily-operated and safe system allowed the operator to control the spindle from either the vicinity of the toolpost or the headstock - and all whilst the motor was left running so that the minimum of time was wasted waiting for speed to build up (it allowed an unladen 12-inch diameter 3-jaw chuck to be accelerated from rest to 1195 r.p.m. In 6 to 7 seconds and braked to a halt in approximately the same time).
The lathe was also fitted with a headstock-mounted emergency stop button that operated through the obligatory 'no-volt' release (to prevent the motor restarting after a power cut), and a motor-run warning light to alert the hard-of-hearing, or those working in a noisy environment, that things were 'active' and the controls should not to be casually played with. The lubrication arrangements for the headstock reflected the hard work the lathe expected to perform and consisted of an impellor-type pump (driven from an extension to the main-motor spindle) that was mounted on a oil tank fitted inside the headstock-end plinth.
From the tank the oil was lifted to a 'distributor block' fastened beneath headstock the headstock's top cover and from there by pipes to the required locations. A flow-indicator sight-glass was fitted to the front face of the headstock to allow the operator to check that the lubricant was flowing correctly. Continued below: Colchester Mascot 8.5-inch (215 mm) centre height lathe Continued: Totally enclosed, the dual Metric/English screwcutting gearbox was lubricated from an oil bath and fitted with hardened and ground gears running on ball-race supported shafts. Three conventional levers together with a 6-position joystick that moved into radial slots around a circle, swapped the ratios. The box was able to generate a wide range of pitches without dismounting or changing any of the changewheels; the range of threads comprised: 40 Metric from 0.4 mm to 14.0 mm; 18 Module from 0.3 to 3.5m; 38 English from 2 to 72 t.p.i. And 27 Diametral from 8 to 60 D.P. The range of sliding feeds varied from 0.002' to 0.032' (0.06 mm to 1.0 mm) and surfacing feeds at half those rates (and thus) from 0.001' to 0.016' (0.03 mm to 0.5 mm) - all per revolution of the spindle.
Doubled walled, with its shafts supported on ball bearing at each end, the apron held gears that were all hardened and ground; the base was closed off to form an oil bath to splash lubricate the internals and at the top of the front face, just to the right of cross-feed screw, was a rod that pushed in to operate a plunger pump to feed the same lubricant to the bed, cross-slide ways and cross-feed nut. Power feeds were selected by a push/pull button and positively engaged by a lever that allowed the feed to be stopped instantly regardless of how deep and heavy the cut was.

A second push/pull button provided a means of reversing either feed whilst a knurled-edge dial, on the apron's right-hand face, allowed the operator to adjust the trip force that disengaged the feed as it was moving to either left or right - so providing a handy means of obtaining maximum accuracy when turning up to a shoulder length. A thread-dial indicator was fitted as standard. The carriage traverse handwheel could be pulled out to disengage it when power feeds were being used - a feature that was included from the very first models and almost certainly included because most examples are found fitted with a rapid carriage return, a vital fitting especially on the long-bed model. The compound slide rest was machined all over and fitted with taper gib strips that allowed a very precise fit to be obtained whilst giving far superior support in comparison with the cheaper 'loose-strip' type. The 11-inch travel cross slide was especially wide and fitted with a cross-feed screw that could be adjusted to reduce backlash; although the slide was devoid of T slots and tapped holes - and so appeared, at a glance, to be incapable of mounting any accessories - the edges of the slide were machines to accept slide-on T-slotted and plain blocks that could hold a variety of items including hydraulic profiling units, and parting-off and other special tools.
Able to be set over, the tailstock held a hardened and ground, 9-inch (229 mm) travel barrel with a huge No. 5 Morse taper.
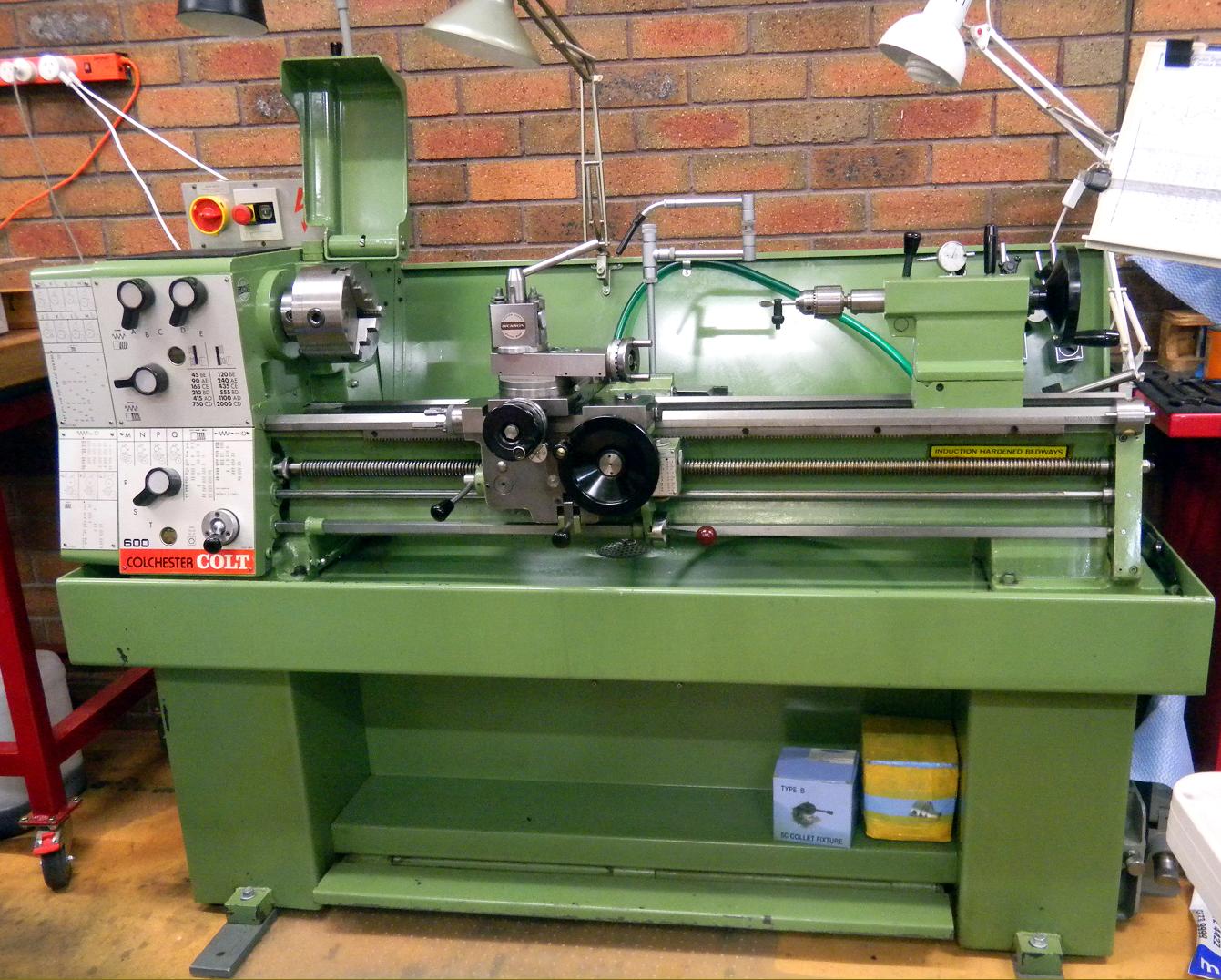
This was engraved with metric and inch graduations - though, surprisingly, considering its use on some smaller Colchester models, there was no zeroing micrometer dial on the feed handwheel. Constructed around two heavy cast-iron plinths, the stand had a usefully deep, slide-out chip tray. However, it offered no storage at all, in either plinths or centre section, even though this would not have been difficult to engineer and would have made life both easier and more productive for the operator.
All but the most perverse would have been happy with the combination of feed and leadscrew combinations offered by the maker for the lathe was available with an English-pitch leadscrew with feed screw micrometer dial graduations in inches or millimetres, or with a Metric leadscrew. Standard equipment supplied with the lathe was fairly sparse and consisted of a 12.5-inch (315mm) 3-jaw chuck, a centre adapter to sleeve down the spindle nose, two No. 5 Morse centres, a simple slotted toolblock to accept one turning tool, driving plate, thread-dial indicator, spanners, oil can, an accuracy and inspection chart and a very useful combined instruction and parts book that showed the whole machine as a set of exploded component diagrams. Accessories included both a 'Super-precision' ductile-iron 12.5-inch (315mm) 3-jaw chuck with a hardened and ground scroll as well as a cheaper 250mm 3-jaw chuck (but still in ductile-iron) with an unhardened scroll and for light-duty use only and of 'limited accuracy'.
A 16-inch (405 mm) ductile-iron heavy-duty 4-jaw chuck and a half-depth body light-duty 12-inch (310 mm) independent 4-jaw chuck were also offered that, like the 3-jaw versions, were all specially made by the Burnerd company.
. These FREE PDF downloads of machine catalogs can help you learn more about your machines and tools, and possibly help you identify them. We have lots of for these machines. If you need any help identifying your machine for a manual, please feel free to submit your machine information with pictures on our page. We also share different machines on our, and display machines that we identify with any addition information we can find. These free pdf catalog downloads can also help you see what kind of accessories were available for your machine and machine specifications.
To view these FREE PDF downloads you need to have Adobe Acrobat reader 10 or later, which is available free here.